Be it your kitchen, vanity, floor, or outdoor space, a colorful tile or slab made of natural stone creates magic and turn all heads. Made of two words ‘natural’ and ‘stone,’ natural stone is a hard material from the lap of Mother Nature.
This stone is simply formed by deposition of water, minerals, and lava over and under the earth over millions of years. Consequently, it isn’t made by engineers who just bring natural stone out of quarries and shape it as per your construction and decoration needs directly. There are lots of natural stone factories in India where stone manufacturers chisel the stone and make it ready to use in the form of cutter slabs, gangsaw slabs, tiles, countertops, and vanities.
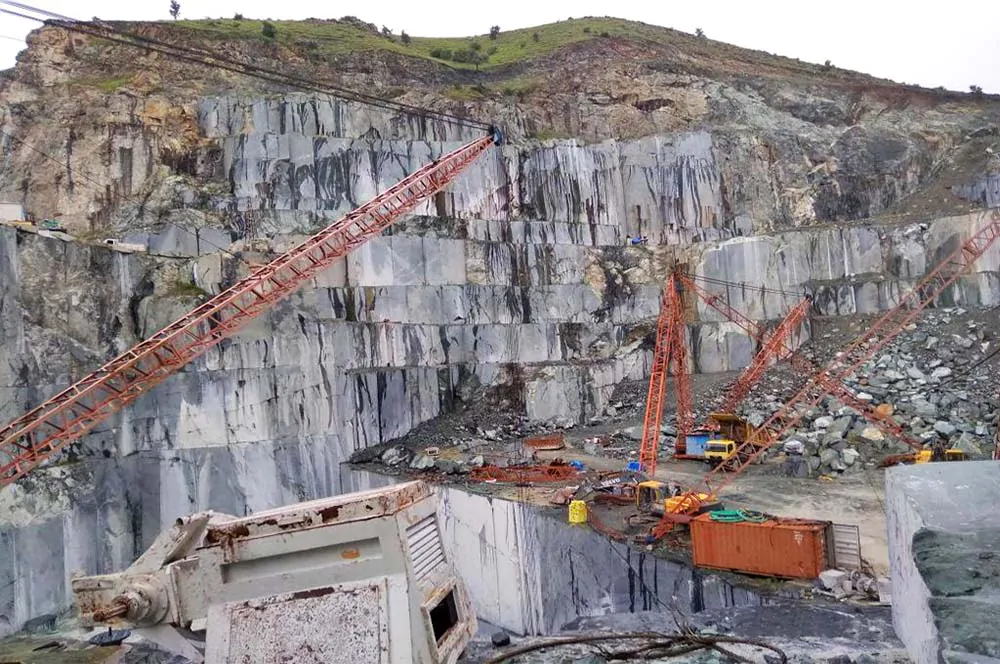
Inherent qualities stones get from nature not engineers
Inherent qualities that stones get from nature, not engineers
All colorful and durable stones you get from stone suppliers are a gift from nature. Before coming to retail shops and stone selling units, the stone comes in the shape of big boulders. Before reaching a factory and coming under the supervision of stone engineers, natural stones come with the following features. Interestingly, these features also remain unchanged with the stone even after many years of practical use. These features include:
- Frost-resistance and slip-resistance
- Low maintenance and long-lasting
- Natural color and antique look
- Sustainable and easily available
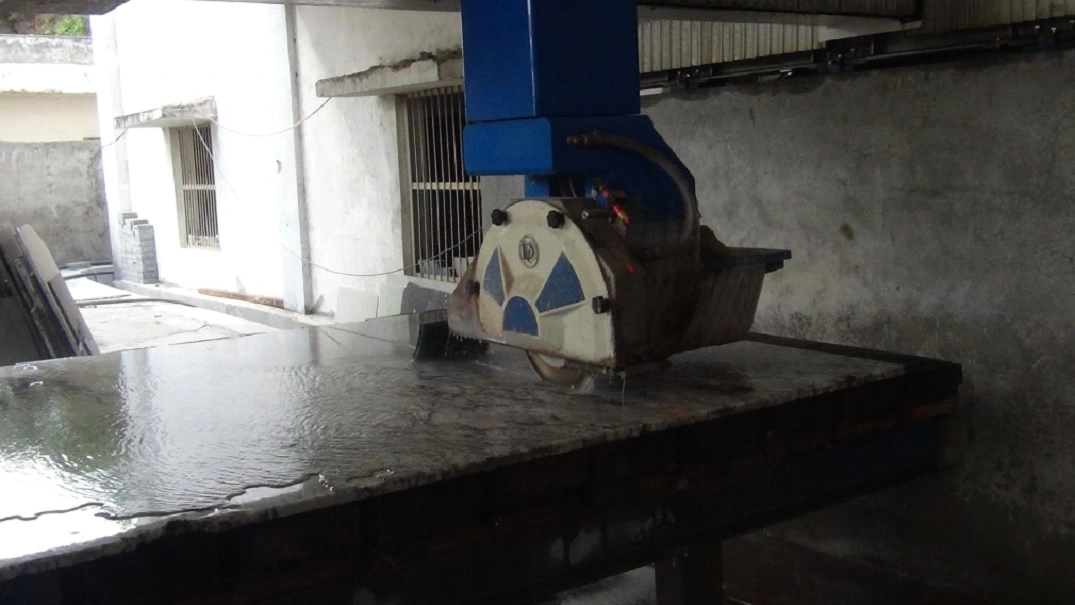
All these remarkable features make natural stones first choice of all homeowners and builders in all parts of the world. These features also make the stone a highly demanding product for domestic and commercial purposes as well. Nature presents its best gift in the form of rough and unpolished granite, marble, quartzite, sandstone, and onyx. Stone processing units refine nature’s gift and make it fit to use. Let’s have a look at how engineers process this stone at processing units before it comes to marble manufacturers and engineers who, in turn, export it to your doorstep.
Engineers make your place more beautiful with processed natural stones
Over thousands of years, natural stones have been used by nearly all the civilizations for myriad applications as a building material. These days, natural stones are a part and parcel of all construction, renovation, and home decoration projects for interiors and exteriors. Thanks to the engineers for giving stones following attributes:
- Timeless beauty and simplicity
- Eco-friendly and aesthetic appeal
- Right size and superior finish
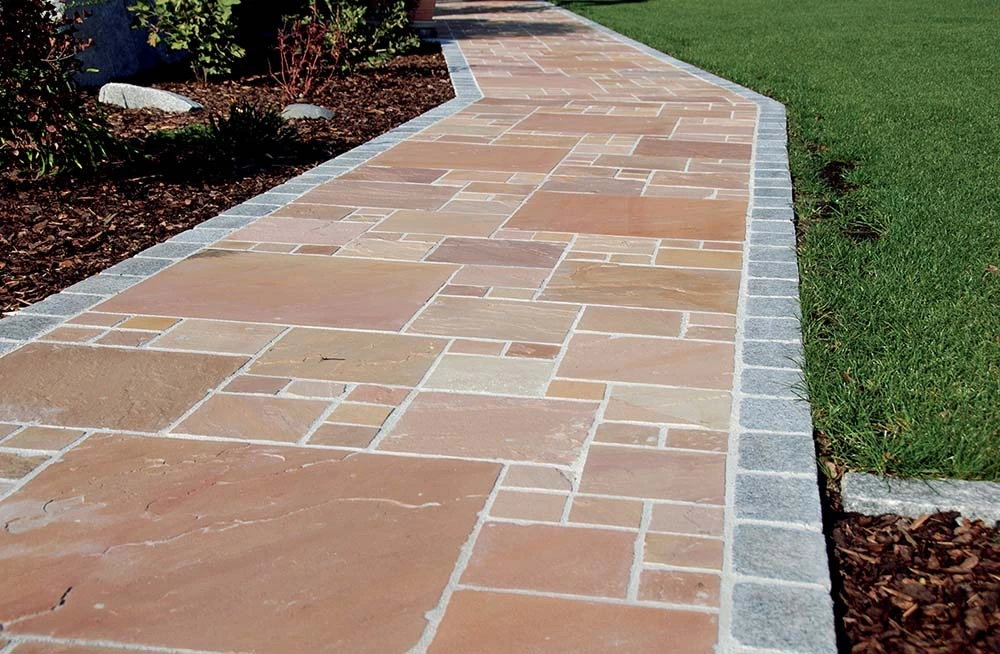
Before the consumer makes a purchase, the stone has to pass through various stages in the processing units owned by a certified Indian natural stone factory. Engineers involved in the task of stone processing abide by the following activities:
Extraction from quarries:
First of all, stone experts quarry out the stone from Rajasthan, Bangalore, and Chennai quarries, without causing any damage to rough materials. The process is initiated with the task of sector wall outlining and using a gas flint that makes long narrow channels. After this, experts dig holes and use explosive cables to set it off. Then, explosives separate the section. Finally, experts use heavy machinery for cutting smaller blocks.
Fabrication process:
Here, machines fabricate the finished product with the tasks of cutting and finishing.
Cut to size:
Experts cut stones to different sizes as per customized orders.
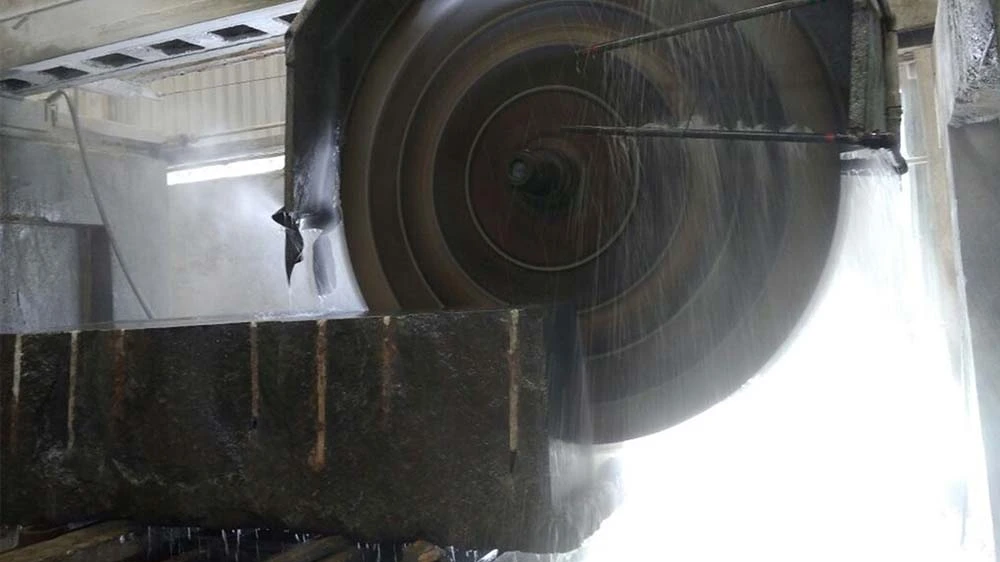
Surface finishing:
Here, expert engineers give natural stones flamed, polished, honed, sandblasted, short-blasted, thermal and tumbled finish.
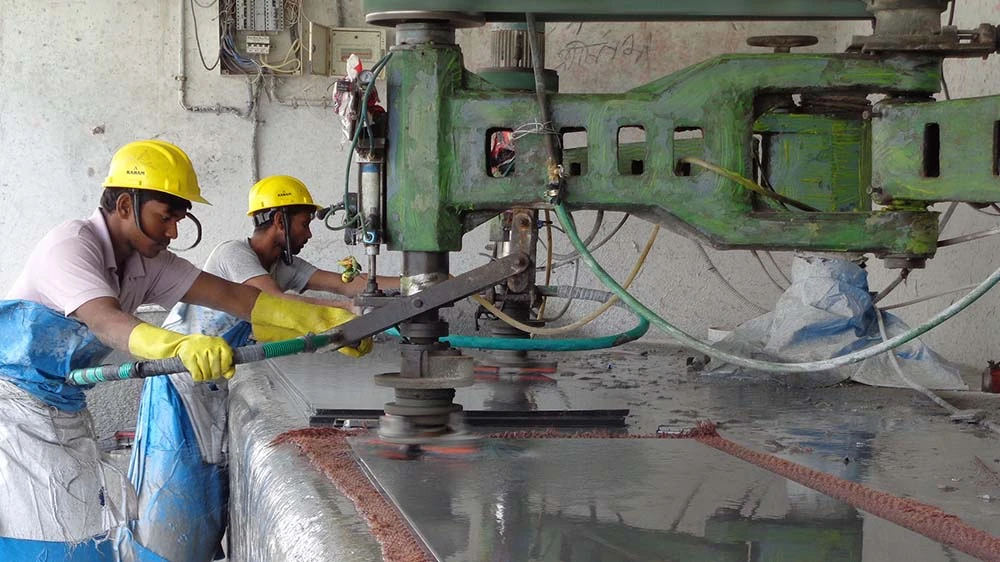
Edging:
It is done when sides are rock-faced.
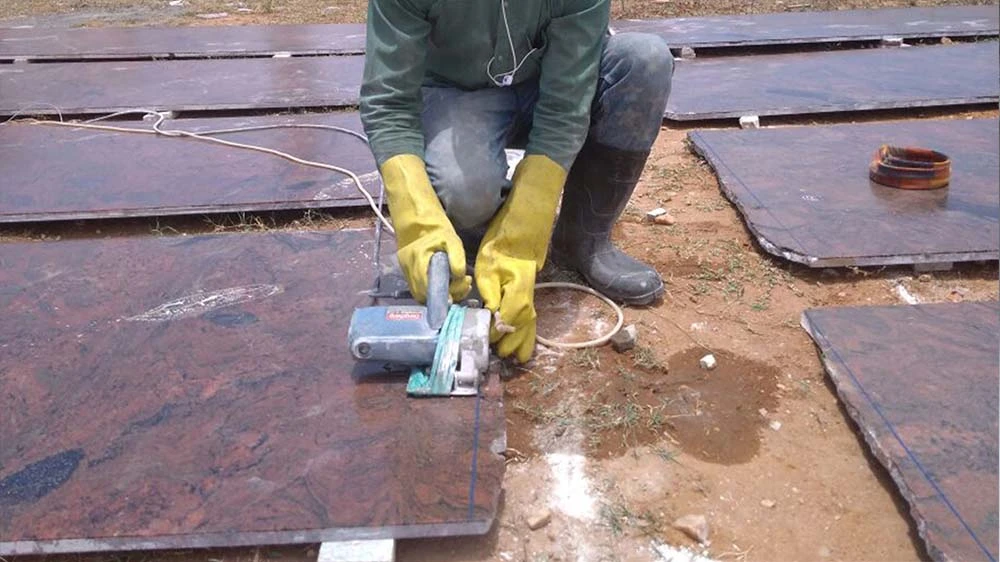
Quality inspection:
Stone engineers follow the quality standards in stone test laboratories to ensure stone’s resistant, compressive strength, density, water absorption, and specific gravity.
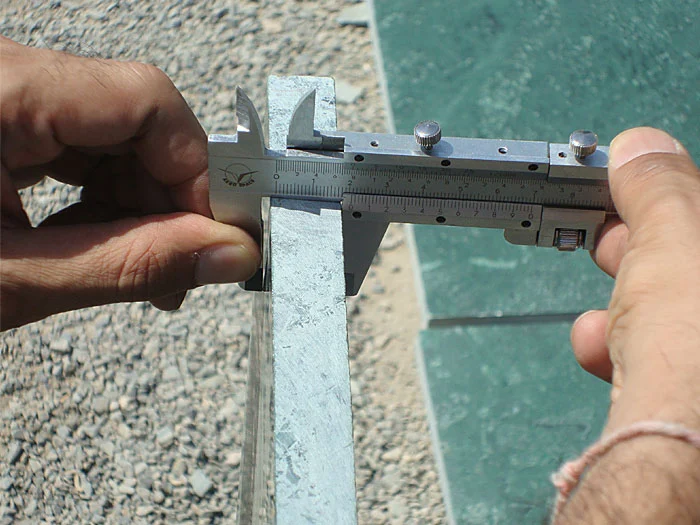
Packaging:
Finally, it is the packaging of final products in wooden crates.
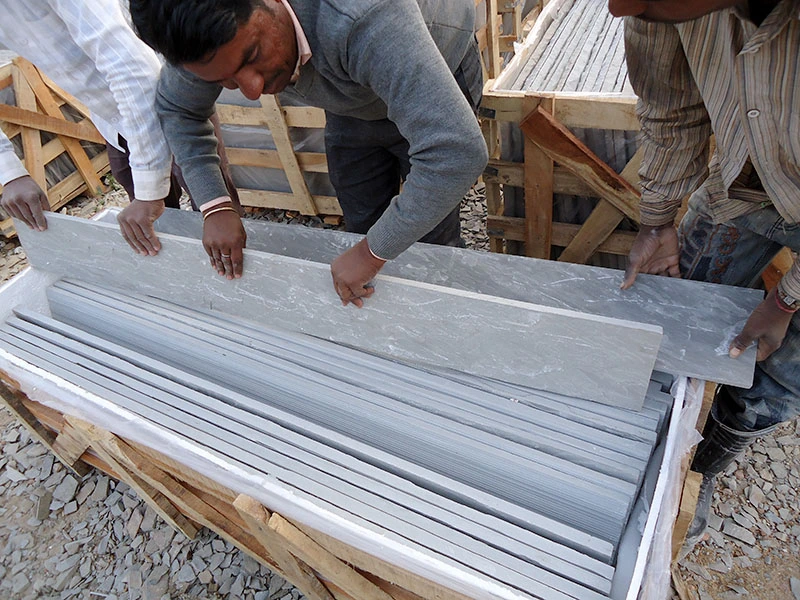
Regatta Universal Exports is a 20-year-old natural stone company serving global granite clientele with high-quality natural products, directly processed from Indian quarries. With two stone processing units in North and South India, the company exports well-processed and polished cutter and gangsaw slabs in multiple size, thickness, and finishes. In addition, it is an affordable price tag that induces a big difference. Here, natural stone engineers process the stone not make it.